Introduction
The world of label production has experienced significant technological advancements over the years, and one area that’s gaining particular traction is laser die-cutting. Traditionally, label die-cutting relied on rotary or flatbed methods, but as demand for precision, flexibility, and speed increases, laser die-cutting has emerged as a game-changer. With its ability to perform intricate cuts without physical tooling, laser technology is revolutionizing how labels are made.
Laser die-cutting technology has come a long way since it first made an appearance at Labelexpo in the mid-1990s. Initially seen as an intriguing but impractical novelty, laser die-cutting has since evolved into a reliable, efficient, and precise method for producing self-adhesive labels. Today, it stands as a testament to how advancements in digital technologies can reshape an entire industry, offering solutions that enhance speed, flexibility, and quality. For label converters and folding carton producers alike, laser die-cutting represents a shift from cumbersome, time-consuming processes to streamlined, tool-less operations that reduce costs, increase productivity, and open new possibilities for intricate designs.
This article will explore the evolution of laser die-cutting, the technology behind it, and its growing impact on the label and packaging industry.
The Early Days of Laser Die-Cutting
The debut of laser die-cutting technology at Labelexpo in the mid-1990s generated significant interest among industry professionals. The concept of using a laser beam to cut labels without the need for physical tools or dies seemed revolutionary, but the early iterations of the technology were far from perfect. These machines were slow and expensive, and they often left unsightly brown edges on the cut materials, particularly around the label’s face. Additionally, waste stripping was not always reliable, which further hampered the machines’ practicality for high-speed production environments.
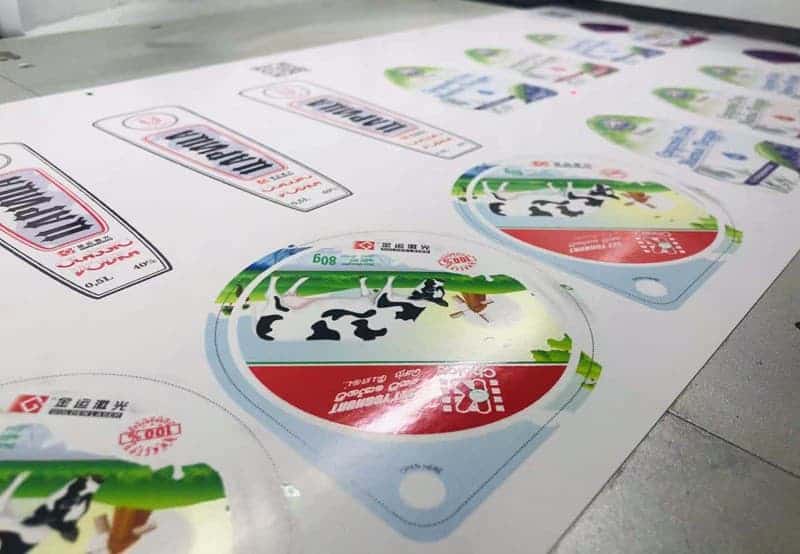
Despite these initial setbacks, the promise of tool-less die-cutting was enough to keep label converters interested. Traditional methods, which required the use of magnetic cylinders and custom dies for each unique label shape, were both costly and time-consuming. Changing a label’s shape meant investing in new dies, which could delay production for days or even weeks. The idea of being able to cut any shape on demand, without the need for expensive and bulky dies, was an appealing prospect for converters looking to reduce setup times and increase flexibility in their production lines.
Technological Evolution Over Time
Over time, laser die-cutting technology improved dramatically. Early issues such as slow speeds and poor cutting quality were addressed through advancements in laser precision, beam control, and software integration. As laser systems became more efficient, they also became more accessible to a wider range of label converters. Machines that once seemed prohibitively expensive began to offer superior capabilities at lower price points, making them an increasingly attractive option for label production.
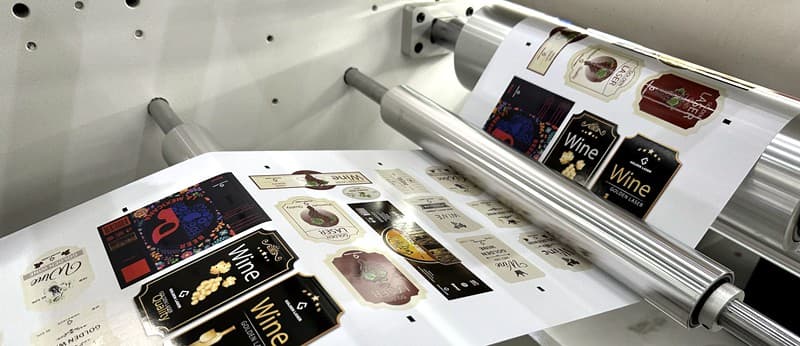
The introduction of digital control systems allowed for more precise beam guidance, enabling the laser to cut intricate shapes with high accuracy. Additionally, improvements in laser power and speed settings; using a CO2 laser with an optimized wavelength, if the material allows, to reduce heat absorption by the material; and implementing air assist during the cutting process can help to eliminate the issue of brown edges, resulting in cleaner cuts and higher overall quality. Modern laser die-cutting systems can now process a wide variety of materials, from self-adhesive labels to 3M VHB tapes, with unprecedented speed and precision.
Benefits of Laser Die-Cutting in Modern Label Production
The key benefits of laser die-cutting technology are what make it so appealing in today’s label production landscape. Let’s explore these advantages in greater detail:
1. Elimination of Tooling Costs
One of the most significant advantages of laser die-cutting is that it eliminates the need for physical dies. Traditional die-cutting processes require dies to be custom-made for each label shape, which can be a costly and time-consuming process. Laser die-cutting, on the other hand, uses a digital process to cut labels directly, with no physical tools required. This means that converters can save money on die production and reduce delays caused by the need to order and wait for new dies.
2. Flexibility and Speed
With laser die-cutting, converters can change label designs on the fly, simply by uploading new digital files to the machine’s software. There’s no need to stop production or swap out physical dies, which allows for much faster turnaround times. This flexibility is especially valuable for converters who work with short-run or custom label jobs, where frequent design changes are necessary. Additionally, laser die-cutting machines are capable of processing multiple jobs in a single run, which further increases productivity and reduces setup time.
3. Reduction in Waste
Laser die-cutting is an entirely digital process, which means there is no need for the trial-and-error adjustments that often accompany traditional die-cutting methods. This results in significantly less waste during the setup phase. In fact, some converters estimate that switching to laser die-cutting has reduced their setup waste by as much as 60%. Given the growing focus on sustainability in the manufacturing industry, this reduction in material waste is a key benefit that can help converters meet their environmental goals.
4. Consistent Quality and Precision
Because laser die-cutting is a non-contact process, there is no risk of cutting tools becoming dull or damaged over time. This ensures that the quality of each cut remains consistent, even during long production runs. Additionally, the precision of modern laser systems allows for the cutting of intricate shapes and designs that would be difficult or impossible to achieve with traditional die-cutting methods. This level of precision is particularly valuable for converters working with complex label designs or materials that require a high degree of accuracy.
How Laser Die-Cutting Works: A Closer Look
At its core, laser die-cutting technology works by directing a high-powered laser beam at the material to be cut. The laser beam is controlled by a computer, which follows a digital file to guide the beam along the desired cutting path. As the laser moves, it vaporizes the material in its path, leaving a clean, high-quality edge behind.
The process can be broken down into several key steps:
1. File Preparation
Before the laser cutting process can begin, the converter must prepare a digital file that contains the design to be cut. This file is typically a vector-based image, which allows the laser cutting software to interpret the exact paths and shapes required for the job. Once the file is ready, it is uploaded to the machine’s software, where the operator can make any necessary adjustments before starting the cutting process.
2. Laser Beam Control
The computer-controlled laser beam is directed at the material to be cut. The power and intensity of the beam can be adjusted based on the thickness and type of material being processed. Modern laser systems are equipped with advanced software that automatically adjusts the beam’s settings to ensure optimal cutting performance.
3. Cutting Process
As the laser beam moves across the material, it vaporizes the material in its path, creating a clean cut with no physical contact. Because the laser cuts by vaporizing the material rather than physically slicing through it, there is no risk of contamination or wear on the cutting tools. This ensures consistent cut quality throughout the production run.
4. Waste Stripping and Finishing
After the cutting process is complete, any excess material (also known as “waste”) is stripped away from the finished labels. Modern laser systems are equipped with waste-stripping mechanisms that make this process quick and efficient, minimizing downtime between jobs.
What Benefits does Laser Die-Cutting offer to Label Converters?
Precision and Flexibility in Label Production
One of the biggest advantages of laser die-cutting is its ability to produce highly precise cuts with intricate detail. This precision allows converters to create complex label designs that would be difficult or impossible to achieve with traditional die-cutting methods. Additionally, because the laser beam is so finely controlled, it can cut through a wide range of materials without damaging them, including delicate or heat-sensitive substrates.
This flexibility makes laser die-cutting an ideal solution for converters working with a variety of materials, from self-adhesive labels to more specialized substrates like carton board, films, or tapes. The ability to easily switch between different materials and designs without needing to change physical dies is a major advantage for converters looking to maximize their production efficiency.
Digital Finishing and Integration with Printing Technologies
Laser die-cutting pairs seamlessly with digital printing technologies, creating a fully automated workflow that can handle both printing and finishing in a single pass. Many converters now use laser die-cutting in conjunction with digital printing presses, such as those produced by Xeikon or inkjet technologies, to streamline their production processes.
The integration of laser die-cutting with digital printing also opens up new possibilities for customization and personalization. For example, a converter could produce a short run of labels with different designs, sizes, or shapes, all within the same production cycle. This level of flexibility is particularly valuable for converters working with custom or short-run orders, where traditional die-cutting methods would be too time-consuming and costly.
Cost and Time Savings for Label Converters
Laser die-cutting offers significant cost and time savings compared to traditional die-cutting methods. Because there are no physical tools to create or maintain, converters can eliminate the costs associated with die production and storage. Additionally, the ability to change designs on the fly reduces downtime between jobs, further increasing productivity.
The time savings are particularly notable for converters who work with short-run or custom jobs, where frequent design changes are required. Traditional die-cutting methods require operators to stop production, swap out dies, and perform test cuts before starting a new job. Laser die-cutting, by contrast, allows operators to simply upload a new digital file and start cutting immediately.
Environmental and Sustainability Benefits
As sustainability becomes an increasingly important consideration for businesses, laser die-cutting offers several environmental benefits. The reduction in material waste, combined with the elimination of physical dies, makes laser die-cutting a more sustainable option compared to traditional die-cutting methods. Additionally, the digital nature of the process means that converters can make design changes without generating excess waste, further reducing their environmental impact.
Types of Laser Cutting: A Versatile Technology
Laser die-cutting technology is capable of performing several different types of cuts, each suited to specific applications:
1. Kiss-Cutting
Kiss-cutting is a technique where the laser cuts through the top layer of material (such as the label face) without penetrating the backing material (the release liner). This is commonly used in the production of self-adhesive labels, where the label must be peeled away from the liner before application.
2. Through-Cutting
Through-cutting is a full-depth cut that penetrates both the label face and the backing material. This technique is used when the entire label, including the liner, needs to be cut into a specific shape.
3. Perforating
Laser die-cutting can also be used to create perforations in labels or other materials. Perforations are often used to create tear-off sections or to allow for easy removal of part of the label.
4. Etching and Engraving
In addition to cutting, laser die-cutting machines can be used to etch or engrave information onto the surface of a label. This includes adding serial numbers, barcodes, or other variable data directly onto the label, all in one pass.
Suitability for a Wide Range of Materials
Laser die-cutting is a highly versatile technology that can be used to cut a wide range of materials, including:
- Self-adhesive labels
- Carton board
- Films and tapes
- Abrasive materials
- Heat-sensitive substrates
However, it is important to note that certain materials, such as PVC, are not suitable for laser die-cutting due to the toxic fumes they release when exposed to the laser. Similarly, aluminum foil cannot be cut with a CO2 laser because its wavelength is too close to that of the laser beam.
Evaluating Laser Die-Cutting Technologies
When considering an investment in laser die-cutting technology, converters should evaluate several key factors, including:
- Speed and throughput: How quickly can the machine process jobs?
- Precision: What level of detail can the machine achieve?
- Material compatibility: Can the machine handle the types of materials the converter works with?
- Ease of integration: Can the machine be easily integrated into existing workflows?
As a key player in the laser die-cutting industry, Golden Laser offers a range of laser die cutting machines with varying capabilities to suit different production needs.
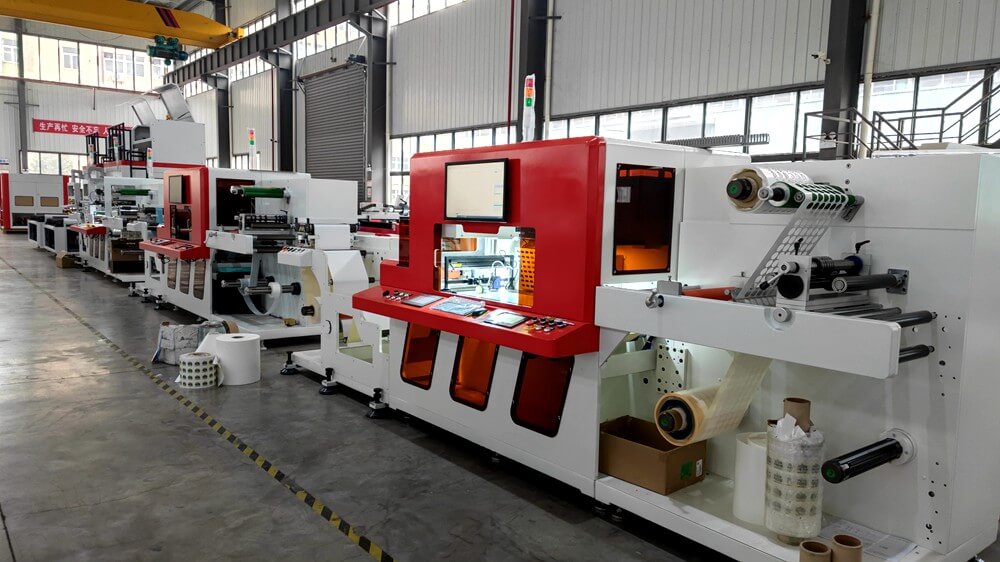
Conclusion
Laser die-cutting has revolutionized the label production industry by offering a faster, more flexible, and more precise alternative to traditional die-cutting methods. As the technology continues to evolve, it is likely to become an increasingly common tool for converters looking to reduce costs, improve efficiency, and offer value-added services to their customers. For those considering an investment in laser die-cutting, the benefits are clear: reduced setup times, lower costs, increased design flexibility, and a more sustainable production process.
FAQs
What materials are compatible with laser die-cutting?
Laser die-cutting works well with materials like self-adhesive labels, carton board, films, tapes, and abrasive materials. However, PVC and aluminum foil are not suitable.
How does laser die-cutting improve efficiency compared to traditional methods?
Laser die-cutting eliminates the need for physical dies, reduces setup times, and allows for rapid design changes, resulting in faster production and lower costs.
Is laser die-cutting suitable for short-run jobs?
Yes, laser die-cutting is ideal for short-run or custom jobs because it allows for quick design changes without the need for new dies.
Can laser die-cutting be integrated with digital printing?
Absolutely, laser die-cutting can be seamlessly integrated with digital printing technologies, allowing for a fully automated workflow from printing to finishing.
What are the environmental benefits of laser die-cutting?
Laser die-cutting reduces material waste and eliminates the need for physical dies, making it a more sustainable option compared to traditional die-cutting methods.
Golden Laser is a leading global provider of laser cutting, engraving, and perforating solutions, offering cutting-edge technology for a wide range of industries. With over two decades of experience, we specialize in delivering innovative and customized laser systems designed to enhance production efficiency, precision, and flexibility. Our machines are trusted by businesses worldwide in sectors such as textiles, automotive, packaging, and electronics. At Golden Laser, we are committed to driving the future of manufacturing through advanced laser technology and exceptional customer service.
Are you interested in integrating laser technology into your production process? We’re here to help!
Explore our wide range of laser cutting machines and custom solutions designed to meet your specific needs.