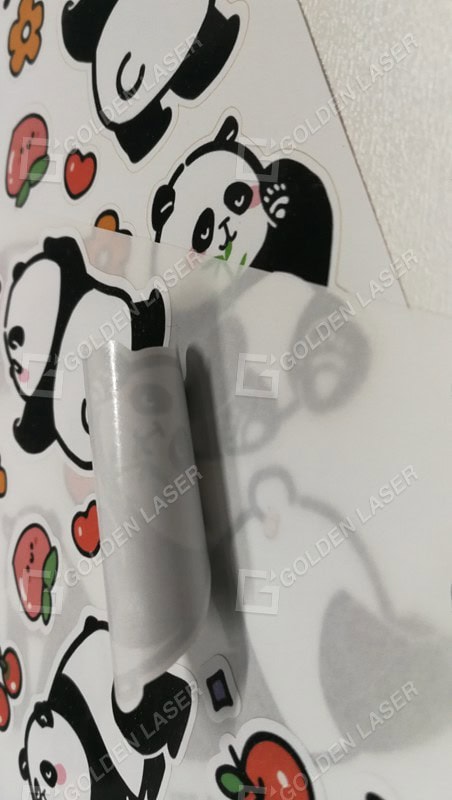
Ever peeled a sticker off its backing with zero effort, and it comes off perfectly clean without disturbing the rest of the sheet? That seamless experience is often the result of a technique called laser kiss cutting. This advanced method uses a highly controlled laser to cut through only the top layer of a material – usually something like PET or paper – without slicing through the backing sheet. It is a precision art form that has become essential in industries needing accurate, repeatable cuts, especially for products like decals, labels, and adhesive components.
But laser kiss cutting is more than just making your sticker sheets look tidy. It is an innovative technology that leverages the pinpoint accuracy of lasers to reduce waste, speed up production, and eliminate the need for expensive physical dies. Whether you are a manufacturer producing thousands of labels or a small business looking for clean, crisp custom designs, laser kiss cutting is an industry game-changer.
Ready to dive into how this works and why it is such a big deal? Let’s explore every angle of laser kiss cutting, from its mechanics to its advantages and beyond.
Understanding the Basics of Laser Kiss Cutting
Definition of Laser Kiss Cutting
Laser kiss cutting is the process of cutting through only the adhesive layer of a material while leaving the backing liner intact. The “kiss” part of the name refers to the gentle contact the laser makes with the material, applying just enough energy to score the surface layer without penetrating the backing. This ensures the cut-out shapes are easily removable, while the rest of the sheet stays whole and protected.
Imagine making perfect paper dolls but only cutting the top sheet, so they stay in place until you peel them off. That’s essentially what kiss cutting accomplishes, except it’s executed with microscopic accuracy and often involves complex shapes and intricate designs.
How Laser Kiss Cutting Differs from Traditional Cutting
Unlike die cutting, which relies on physical metal dies to stamp out shapes, laser kiss cutting uses a beam of concentrated light. This brings several benefits:
• No physical tools required, reducing wear and tear.
• Greater flexibility for design changes – just update the software.
• Extreme precision, even for tiny, delicate, or complex designs.
Traditional cutting methods also often apply too much pressure, leading to damage to the backing layer or uneven cuts. Laser kiss cutting avoids this, making it perfect for high-end products where perfection is non-negotiable.
How Does Laser Kiss Cutting Work?
Key Components of the Laser Kiss Cutting Process
At the heart of laser kiss cutting are a few essential elements:
• Laser Source: Typically CO2 lasers are used because they work excellently with non-metallic materials.
• Optical System: Mirrors and lenses focus the laser to an ultra-fine point for precise cutting.
• Material Feed System: Ensures the material is smoothly transported under the laser for continuous cutting.
• Control Software: Manages the design, speed, power, and depth of the cut.
These components work together seamlessly, ensuring the laser interacts with the material with just the right amount of intensity and speed.
Step-by-Step Process Explanation
1. Design Upload: The desired cut pattern is loaded into the machine’s software.
2. Material Positioning: The material (e.g. adhesive-backed paper or PET) is aligned on the cutting bed.
3. Laser Calibration: Power and speed settings are adjusted based on the material thickness.
4. Cutting: The laser follows the programmed path, gently “kissing” through the top layer.
5. Quality Check: Operators inspect the final product to ensure perfect cuts without damaging the backing.
6. Collection: Finished sheets are either stacked, rolled, or prepared for the next production stage.
Advantages of Laser Kiss Cutting
Laser kiss cutting offers numerous advantages over traditional cutting methods, such as mechanical die cutting or knife cutting:
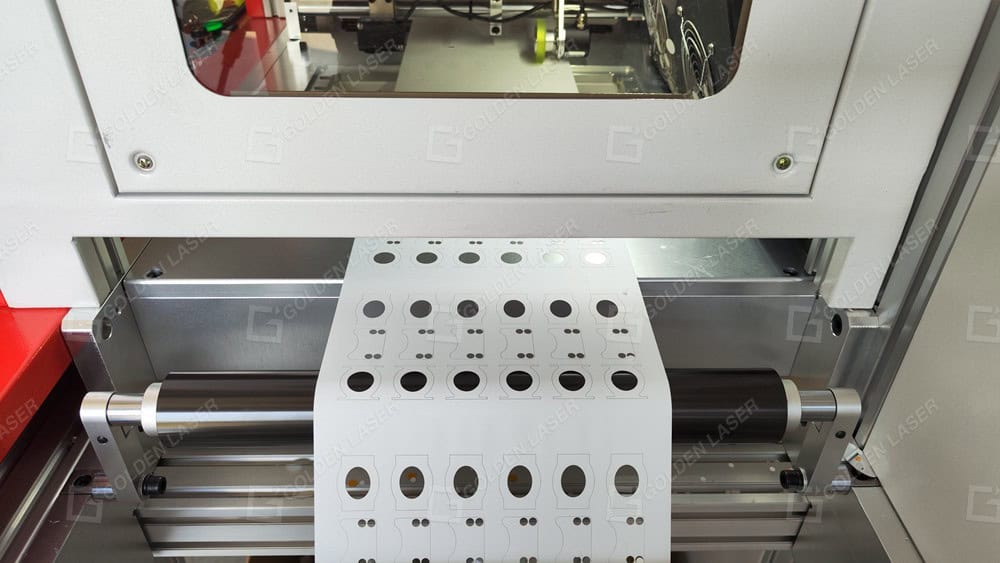
Precision and Accuracy: Laser cutting provides unparalleled precision and accuracy. The focused laser beam can create extremely fine details and intricate shapes that would be impossible to achieve with mechanical cutting tools. The non-contact nature of the process also minimizes material distortion.
Non-Contact Cutting: Because the laser beam does not physically touch the material, there is no risk of mechanical stress, tearing, or deformation. This is particularly important for delicate materials or those with intricate designs. It also eliminates the need for sharp blades, reducing the risk of injury.
Minimal Material Waste: Laser cutting is a very efficient process, producing minimal material waste. The laser beam’s narrow kerf (the width of the cut) and the ability to nest designs closely together on the material sheet maximize material utilization.
Versatility: Laser kiss cutting can be used on a wide variety of materials, including paper, cardstock, vinyl, film, textiles, foam, rubber, and some thin metals. This versatility makes it suitable for a broad range of applications.
Speed and Efficiency: Laser cutting is generally faster than traditional cutting methods, especially for complex designs. The high speed of the laser beam and the automated nature of the process contribute to increased throughput and reduced production times.
Clean Edges: Laser cutting produces clean, smooth edges with minimal burring or fraying. This often eliminates the need for secondary finishing processes, further improving efficiency.
Reduced Tooling Costs: Unlike die cutting, which requires the creation of custom dies for each design, laser cutting is a tool-less process. This eliminates the cost and lead time associated with die manufacturing, making it ideal for short runs, prototypes, and custom designs.
Rapid Prototyping: Laser cutting allows for quick and easy design changes. Modifications can be made to the digital design file and implemented immediately, without the need to create new physical tools. This makes laser cutting an excellent choice for rapid prototyping and product development.
Flexibility: Laser cutting systems can easily switch between different cutting patterns and materials. This makes it easy to handle a variety of jobs without significant downtime or setup changes.
Automation: Laser kiss cutting can easily integrate with automated work flows.
Common Applications of Laser Kiss Cutting
Laser kiss cutting is used in a wide range of industries and applications, including:
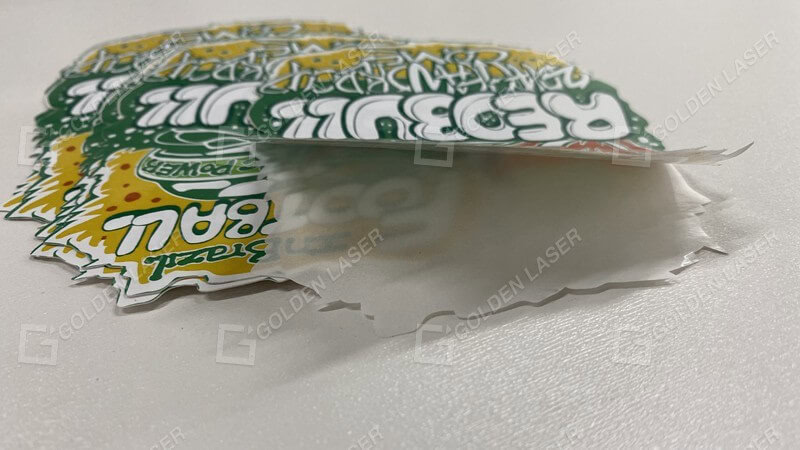
Labels and Stickers: This is perhaps the most common application of laser kiss cutting. It’s used to create custom-shaped labels and stickers for products, packaging, branding, and promotional purposes. The ability to cut intricate designs and precisely control the cutting depth makes it ideal for this application.
Packaging: Laser kiss cutting is used to create custom packaging components, such as boxes, inserts, and labels. It allows for precise cutting of intricate shapes and designs, enhancing the visual appeal and functionality of the packaging.
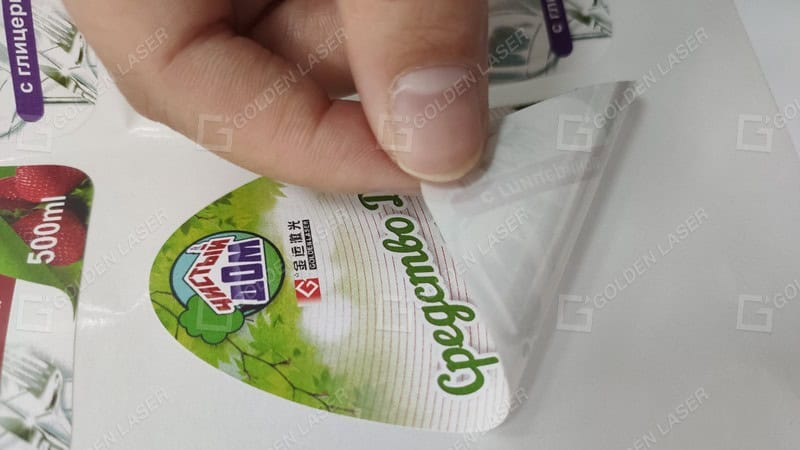
Gaskets and Seals: Laser kiss cutting can be used to create precise gaskets and seals from materials like rubber, foam, and cork. The non-contact nature of the process ensures that the material is not compressed or deformed during cutting.
Medical Devices: The precision and cleanliness of laser kiss cutting make it suitable for creating components for medical devices, such as wound dressings, medical adhesives, and diagnostic tools.
Electronics: Laser kiss cutting is used in the electronics industry to create flexible circuits, adhesive tapes, screen protectors, and insulating materials. The ability to cut delicate materials without damage is crucial in this application.
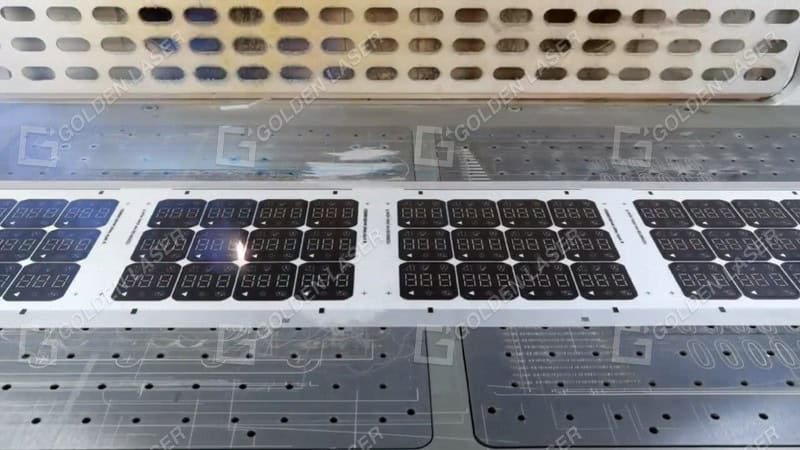
Automotive: Laser kiss cutting is used to create interior and exterior components for automobiles, such as gaskets, seals, labels, and decorative trim.
Aerospace: Similar to the automotive industry, laser kiss cutting is used in aerospace for creating precision components, including gaskets, seals, and insulating materials.
Signage and Printing: Laser kiss cutting is used to create intricate designs for signage, banners, and promotional materials. It allows for precise cutting of various materials, including vinyl, paper, and acrylic.
Textile and Fashion: Laser kiss cutting can be used to create intricate patterns and designs on fabrics. It’s also used for creating appliques, labels, tackle twill, and other textile decorations and components.
Arts and Crafts: Laser kiss cutting is increasingly popular in the arts and crafts industry for creating custom stencils, cards, invitations, and other decorative items.
Adhesive Tapes: Creating custom shapes and sizes of adhesive tapes for various applications.
Abrasives: Cutting abrasive materials to specific shapes for sanding and finishing applications.
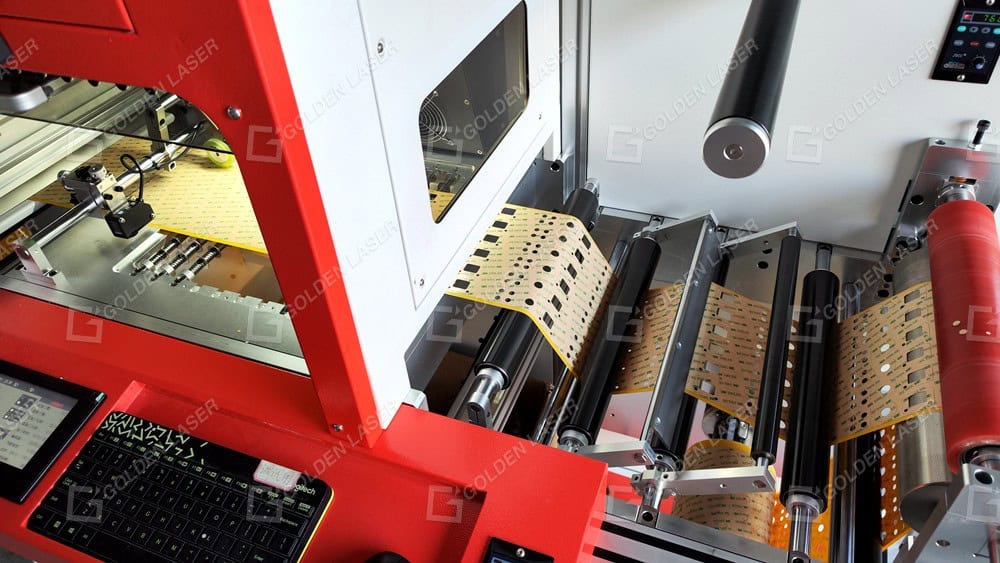
Materials Compatible with Laser Kiss Cutting
One of the best things about laser kiss cutting is its versatility across a broad range of materials. Whether you’re working with thin films, flexible sheets, or delicate adhesives, laser kiss cutting can handle it with ease. Some of the most commonly used materials include:
Adhesive Materials:
- Self-adhesive tapes and films
- Double-sided adhesive sheets
- Pressure-sensitive adhesives (PSA)
- Protective films and foils
Paper and Cardstock:
- Paper labels and stickers
- Cardboard
- Paperboard
- Greeting cards
Plastics:
- Thin plastic sheets
- Polyesters
- Polypropylene
- Polyethylene
- Polyimide (Kapton®)
- Polyester (Mylar®)
Films and Foils:
- Heat Transfer Vinyl
- Polyester film
- Mylar
- Thin metal foils (aluminum, copper)
Fabrics and Textiles:
- Apparel fabrics
- Upholstery materials
- Leather
- Synthetic textiles
- Canvas
- Cotton, silk, and wool
Foam and Rubber:
- Foam materials
- Sponge rubber
- Neoprene
- Silicone rubber
- Expanded polystyrene or polypropylene foams
- Depron modeling foam
- Foam-cored boards
- EVA foam
Gaskets and Seals:
- Gasket materials (paper, rubber, cork)
- Seal materials
- Insulation materials
Other materials:
- Non-wovens
- Medical tapes
- Adhesive components for electronics
- Protective films for screens and displays
Comparison of Laser Kiss Cutting vs. Die Cutting
Benefits Over Die Cutting
While both laser kiss cutting and die cutting are used to create cut shapes, they differ significantly in their processes and capabilities. Here’s a comparison:
Feature | Laser Kiss Cutting | Die Cutting |
---|---|---|
Tooling | No tooling required | Requires custom-made dies for each design |
Precision | Extremely high precision and accuracy | Lower precision, especially for intricate designs |
Versatility | Can cut a wide variety of materials | Limited material compatibility, especially for delicate or thick materials |
Setup Time | Short setup time | Longer setup time due to die creation and mounting |
Cost | Lower cost for short runs and prototypes; higher cost for very large volumes due to slower speed compared to die cutting | Higher initial cost due to die creation; lower cost per unit for very large volumes due to high-speed stamping process |
Design Changes | Easy and quick design changes | Design changes require new dies, increasing cost and lead time |
Material Waste | Minimal material waste | Can result in more material waste, especially for complex shapes |
Speed | Generally faster than die-cutting for short to medium runs and complicated designs. | Faster for very large, simple-shape production runs. |
Choosing the Right Cutting Method
The best cutting method – laser kiss cutting or die cutting – depends on the specific application and requirements.
Choose Laser Kiss Cutting if:
- You need high precision and intricate designs.
- You are working with delicate or flexible materials.
- You have short runs or require frequent design changes.
- You need quick turnaround times.
- You are working with a variety of materials.
- You want to minimize material waste.
Choose Die Cutting if:
- You have very large production volumes.
- The design is relatively simple.
- Material cost is a primary concern.
- High speed is the most important factor.
- You are working with thicker, more rigid materials.
Conclusion
Laser kiss cutting is more than just a modern marvel – it is a necessity for businesses needing precision, efficiency, and adaptability. From delicate labels and intricate decals to medical-grade adhesives and automotive components, laser kiss cutting stands out as the top choice for high-quality, high-volume, and highly customized cuts. Its ability to work across materials, reduce waste, and integrate seamlessly with automated systems has made it an industry leader. As technology advances, expect this process to become even more vital in manufacturing, packaging, and design.
So whether you’re just getting started with laser cutting or you are looking to refine your production, understanding its advantages, applications, and innovations will give you a clear edge in today’s fast-paced market.
Golden Laser is committed to providing laser cutting solutions to help businesses optimize their production processes and create high-quality products. Contact us today to learn more about how our laser cutting machines can benefit your business.