Laser cutting is increasingly being utilized across a wide variety of materials and industries, offering a highly efficient alternative to traditional cutting methods. This approach is well-suited for both small production runs and large-scale industrial manufacturing. The key advantage of laser cutting lies in its contactless processing, making it particularly valuable for delicate materials in the textile industry. Every day, more applications emerge, showcasing the growing significance of laser cutting technology in the textile market.
What is filtration?
Industrial textiles represents a significant application area of technical textiles, catering to chemical, electrical, and mechanical engineering needs, including filtration processes.
Filtration, as a mechanical or physical operation, is designed to separate solids from fluids (liquids or gases) by using a medium that allows only the fluid to pass through. Oversized solids in the fluid are retained, but the separation is rarely absolute; the solids may retain some fluid, and the filtrate might contain fine particles, depending on the filter’s pore size and thickness.
Filtration is commonly used to separate particles and fluids in a suspension, where the fluid can be a liquid, gas, or supercritical fluid. Depending on the application, the process can isolate either the fluid, the solids, or both. It is a crucial unit operation in chemical engineering, often integrated with other processes, as seen in bio-filters that combine filtration with biological digestion.
Each type of filter fabric is tailored for specific applications, climatic conditions, and operating environments to achieve optimal output and efficiency. As we look to the future, filter fabric will play a pivotal role in everyday life. No single fabric type can serve all filtration applications; the choice of fabric depends on the intended use.
Why use laser to cut filter fabric?
The ability to digitally customize the size and shape of technical textiles for filtration purposes is becoming increasingly important. Laser technology stands out as the only solution capable of achieving this customization with unparalleled precision and quality. Its advanced capabilities make it indispensable for producing high-performance technical textiles that meet the demands of diverse and critical applications.
A significant portion of filter media, particularly those made from non-woven fabrics, falls under the category of technical textiles and can typically be shaped using knives or conventional cutting tools. However, challenges arise when filtration processes need to adapt to changing operational requirements, often necessitating small or medium production runs. In such cases, traditional methods quickly hit their limits in terms of flexibility.
Laser technology offers a compelling solution, enabling the customized fabrication of filters, including large-scale ones, while ensuring the immediate availability of materials to operators. One of the standout advantages of laser technology is its contactless processing, which prevents material deformation and ensures clean, precise cuts. This high-precision capability makes lasers an ideal choice for producing filters that meet the exacting demands of modern filtration systems.
CO2 laser systems for filter cloth cutting from Golden Laser
With a strong specialization in CO2 laser systems for cutting non-metallic materials, Golden Laser has firmly established itself as a global leader in the market. Automation has become indispensable for economical textile processing, and Golden Laser addresses this need with its advanced Conveyor System designed for roll material handling.
This innovative system enables textiles to be fed directly from the roll into the laser cutting process and then routed seamlessly to a table extension after cutting. With high-precision material alignment during feed cycles, it is possible to produce virtually endless sections with exceptional accuracy. The roll material is fed through an automatic feeding unit, while an edge controller ensures precise positioning of the material during processing.
For further automation, an optional winding unit can be integrated into the Conveyor System. This unit efficiently winds the processed textiles, resulting in a fully automated cutting process from start to finish. By combining precision, efficiency, and automation, Golden Laser offers state-of-the-art solutions for textile processing, meeting the demands of modern manufacturing.
The flexibility and adaptability of laser systems have always been a guiding principle in their development. With users’ evolving needs in mind, our latest models are engineered with a modular design. This forward-thinking approach ensures that each system can be tailored to specific applications, offering customized solutions that grow with your business and adapt to diverse production demands.
For textile processing, we have introduced an innovative table design optimized for precision and efficiency. This table features a stainless steel wire mesh that excels in supporting thin and flexible materials during the cutting process. Not only does this mesh provide a stable surface for machining, but it also serves as an essential component of the conveyor system, seamlessly transporting materials through the workflow. This dual functionality enhances productivity, especially for continuous processing of large textile rolls.
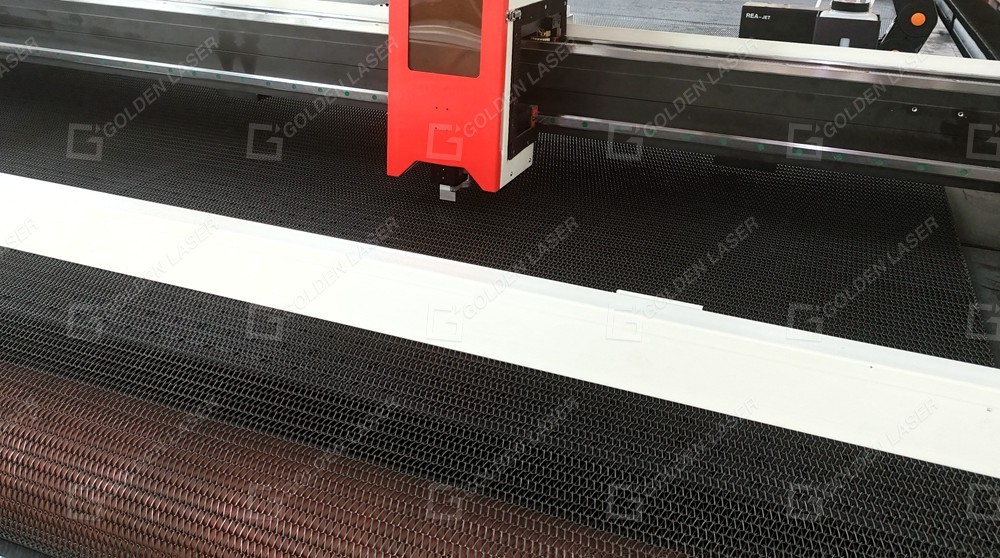
To further enhance the versatility of our laser systems, Golden Laser offers an advanced Ink Marker as an optional upgrade. Designed for seamless retrofitting, this marking system meets the growing demand for economical, non-contact marking methods in industries such as textile manufacturing. Perfect for creating sewing guides, clippings, and other markings, the Ink Marker employs a compressed-air-driven universal jet system. It uses a refillable ink cartridge, making it both cost-effective and environmentally friendly. The system can be adjusted to produce line widths between 2 mm and 4 mm, offering excellent precision for a wide range of applications. Compatible with materials like polyester, polypropylene, acrylic, and most natural textiles, the Ink Marker ensures sharp, durable markings, enhancing workflow efficiency and product quality.
Advantages of Laser Cutting for Filters
1. Automatic Sealing of Cutting Edges
Prevents fraying by seamlessly sealing edges during the cutting process, ensuring durability and maintaining the quality of the filter material.
2. No Tool Wear
Unlike mechanical cutting methods, lasers do not suffer wear and tear, ensuring consistent quality over long-term use and reducing maintenance costs.
3. High Flexibility
Laser systems offer extensive flexibility in daily operations, with numerous additional options and features to adapt to varying production needs.
4. High Precision and Repetition Accuracy
Guarantees precise, consistent results across multiple cutting tasks, crucial for maintaining strict quality standards in filter production.
5. Virtually Dust-Free Cutting
Provides a clean and efficient process, minimizing contamination and ensuring a hygienic final product.
6. Optimal Material Utilization
Maximizes the use of material with precision cutting, reducing waste and lowering overall production costs.
7. Non-Contact Cutting Process
Eliminates the application of force, avoiding material distortion caused by stretching or punching, ideal for delicate filter materials.
8. Large Format Cutting
Accommodates roll widths of up to 3,500 mm, enabling efficient processing of large-format materials for industrial-scale production.
9. Optional Automation
Features such as automatic material feed and winding system enhance workflow efficiency, reduce manual intervention, and increase overall productivity.
Conclusion
With a strong specialization in CO2 laser systems for cutting non-metallic materials, Golden Laser has firmly established itself as a global leader in the market. Automation has become indispensable for economical textile processing, and Golden Laser addresses this need with its advanced Conveyor System designed for roll material handling.