The automotive industry is in constant pursuit of enhanced comfort, safety, and aesthetic appeal, and the seating system plays a pivotal role in achieving these goals. Modern car seats are sophisticated assemblies, often incorporating diverse materials like leather, synthetic fabrics, foam, and even integrated technologies for heating and ventilation. Manufacturing these intricate components with both efficiency and precision demands advanced technologies, and laser cutting has emerged as a transformative solution. As we delve into the application of laser cutting in automotive seating, exploring its myriad benefits, it’s worth noting that companies like Wuhan Golden Laser Co., Ltd. are at the forefront of providing these cutting-edge solutions to the industry. This article will explore the advantages, applications and provider of choice.
The Advantages of Laser Cutting in Automotive Seating
Traditional methods for cutting materials used in car seats, such as die-cutting, have limitations. Die-cutting requires physical dies for each pattern, leading to significant tooling costs, storage requirements, and inflexibility when design changes are needed. It also can produce subpar cutting effects, and material waste. Laser cutting offers a superior alternative, bringing numerous advantages:
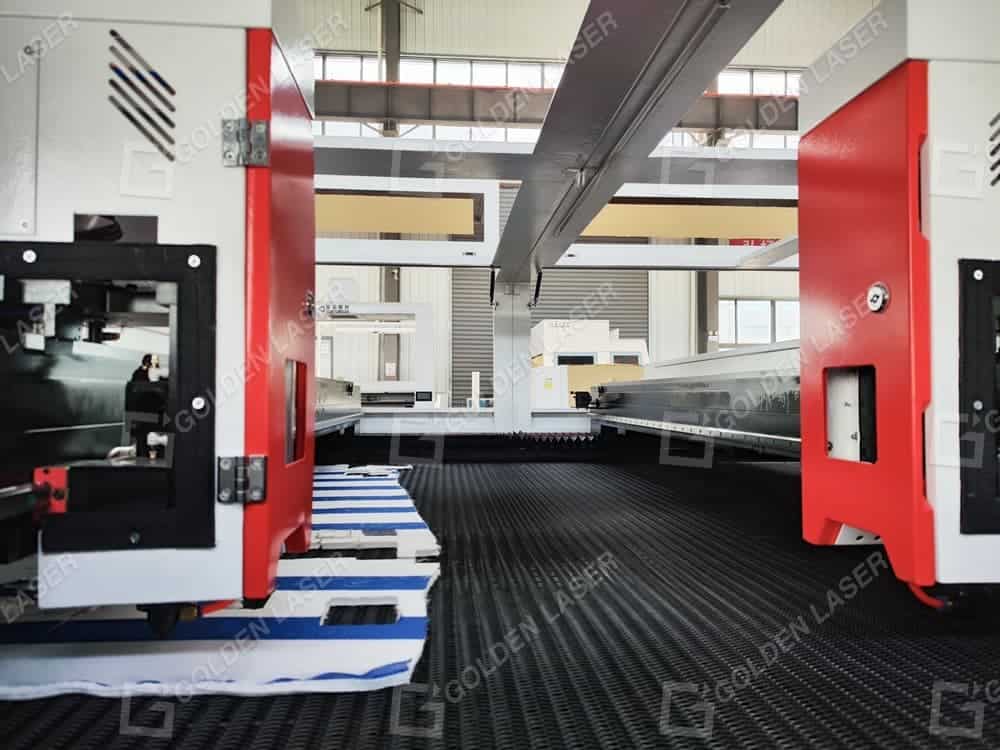
Unmatched Precision and Accuracy
Laser cutting utilizes a highly focused beam to cut materials with extreme precision. This is crucial for car seat manufacturing, where intricate designs, complex shapes, and tight tolerances are often required. The computer-numerical control (CNC) technology integrated into laser cutting systems ensures consistent and accurate cuts, minimizing errors and ensuring perfect fit and finish. This precision also allows for intricate designs and patterns to be cut into the seat material.
Increased Efficiency and Speed
Laser cutting is significantly faster than traditional methods. The non-contact nature of the process, combined with high cutting speeds, accelerates production cycles. This leads to reduced lead times and increased throughput, allowing manufacturers to meet growing demands efficiently.
Material Versatility
Laser cutting systems can handle a wide range of materials used in car seat manufacturing. This versatility is a significant advantage, allowing manufacturers to work with diverse materials and designs without needing to switch between different cutting tools.
Reduced Material Waste
The precision of laser cutting minimizes material waste. Advanced nesting software optimizes the placement of patterns on the material, maximizing material utilization and reducing scrap. This not only saves costs but also contributes to more sustainable manufacturing practices.
Clean and Sealed Edges
For synthetic materials, laser cutting offers the added benefit of producing clean, sealed edges. The heat from the laser melts and fuses the edges, preventing fraying and eliminating the need for additional finishing processes. This is particularly beneficial for materials like polyester and other synthetic fabrics.
Flexibility and Customization
Laser cutting systems offer unparalleled flexibility in design and customization. Manufacturers can easily create custom designs and patterns, catering to individual customer preferences or specific vehicle models. This flexibility is essential in today’s market, where personalization is increasingly important. The ability to easily make changes to designs during the R&D stage is highly beneficial.
Contactless process
No pressure is put on the material so there is far less chance of distortion of the materials.
Simplified Workflow
The laser cutting process simplifies the entire workflow, from design to production. With traditional methods of manufacturing heated car seats, for example, cutting the cushions and stitching the conductive wires was time-consuming. The laser cutting machine simplifies the manufacturing steps, improves production efficiency, and saves material and time.
Materials Used in Car Seat Manufacturing and Laser Cutting Suitability
Car seats are made from a variety of materials, each with its own properties and requirements. Laser cutting is suitable for many of these materials, including:
3D Mesh Cloth and Spacer Fabric
These materials, often used for ventilation and comfort, can be effectively cut with laser systems. The precision of the laser ensures that the intricate structure of these materials is maintained.
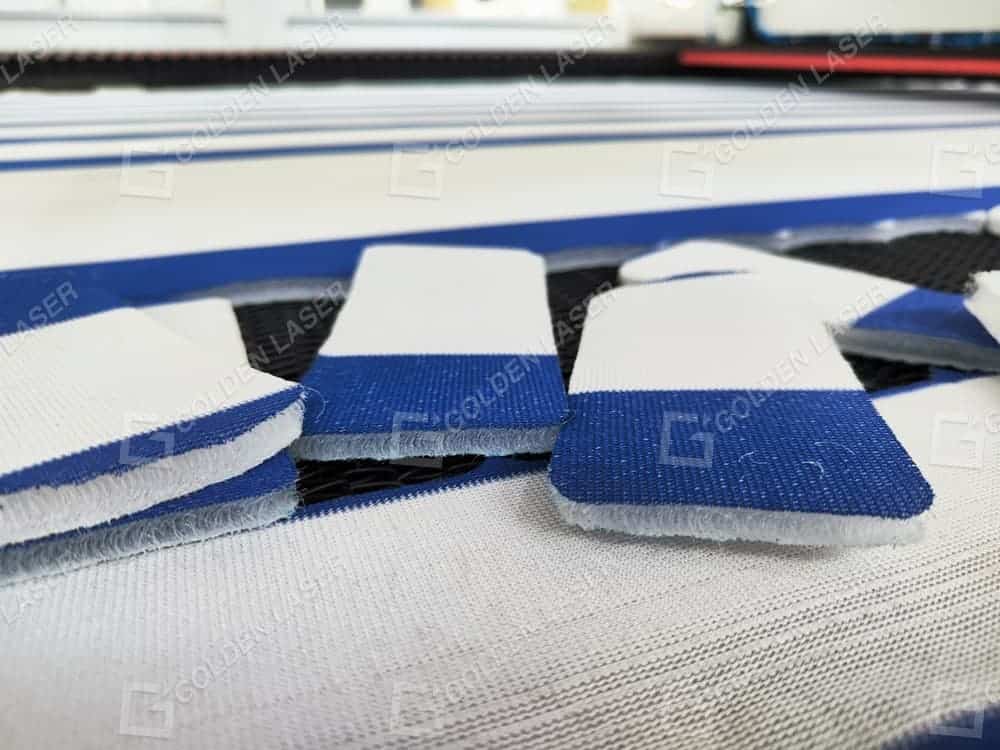
Fabrics (Woven and Non-woven)
Various fabrics, including polyester, nylon, and spacer fabrics, are commonly used in car seat construction. Laser cutting provides clean cuts and, in the case of synthetics, sealed edges, preventing fraying.
Leather and Synthetic Leather
Laser cutting is ideal for both natural and synthetic leather. It provides clean, precise cuts without damaging the material. The non-contact nature of the process prevents any distortion or marking of the leather.
Foam
Certain types of foam can be laser cut, although careful consideration must be given to the type of foam. Polystyrene foam, for example, is not recommended for laser cutting due to its flammability and tendency to melt and leave deposits. However, other foams can be processed successfully, allowing for precise shaping and contouring.
Other materials
Other materials that can be laser processed include non-woven fabrics and glass fiber composite materials.
It’s essential to choose the correct laser type and parameters for each material to achieve optimal results. CO2 lasers are generally preferred for cutting organic materials like leather, fabrics, and some foams, while fiber lasers are better suited for metals, though certain fiber lasers can also be adapted for some non-metal applications.
Applications of Laser Cutting in Automotive Seating
Laser technology finds various applications within the automotive seating manufacturing process:
Seat Cover Cutting
Laser cutting precisely cuts the various panels that make up a seat cover, ensuring a perfect fit and minimizing material waste.
Perforation
Laser perforation creates precisely sized and spaced holes in seat covers for ventilation and aesthetic purposes. This is particularly important for leather seats to enhance breathability.
Heated Seat Integration
Laser cutting can be used to create precise channels or cutouts in the seat materials to accommodate heating elements, ensuring seamless integration and optimal heat distribution.
Airbag Integration
Some seating systems incorporate airbags. Laser cutting can be used to create weakened seams or specific patterns that allow for controlled airbag deployment.
Customization and Personalization
Laser cutting enables manufacturers to easily create custom designs, patterns, and logos on seat covers, offering a high degree of personalization.
Golden Laser: A Leader in Automotive Seating Laser Solutions
Wuhan Golden Laser Co., Ltd. (Golden Laser) is a leading manufacturer of laser equipment, specializing in providing digital, intelligent, and automated laser application solutions. Established in 2005 and listed on the Shenzhen Stock Exchange in 2011, Golden Laser has become a world-renowned brand, particularly in the field of textiles, clothing, and industrial flexible fabric laser applications.
Golden Laser offers a comprehensive range of laser cutting machines specifically designed for the automotive industry. Their machines are known for their:
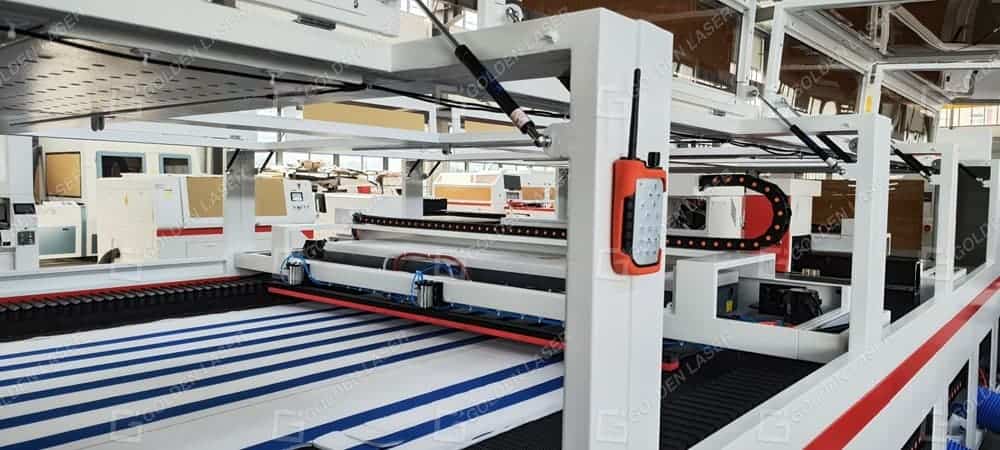
High Precision and Speed
In textile industry, Golden Laser machines utilize advanced CO2 laser technology and high-quality components to deliver exceptional cutting accuracy and speed.
Robust Construction
Golden Laser machines are built to withstand the demands of industrial production environments.
User-Friendly Software
Golden Laser software is intuitive and easy to use, allowing for quick design implementation and efficient machine operation.
Customization Options
Offer a variety of machine configurations and customization options to meet specific customer needs.
Comprehensive Support
Golden Laser provides excellent customer support, including training, maintenance, and technical assistance.
Future Trends in Laser Cutting for Automotive Interiors
The application of laser cutting in car seat manufacturing is expected to continue to grow and evolve. Several key trends are shaping the future of this technology:
Increased Automation
Greater integration of robotics and artificial intelligence (AI) will further automate the laser cutting process. This includes automated material loading and unloading, real-time cutting parameter optimization, and predictive maintenance.
3D Laser Cutting
3D laser cutting systems are becoming more prevalent, allowing for the cutting and welding of complex three-dimensional components. This opens up new possibilities for car seat design and functionality.
Enhanced Speed and Power
Laser cutting machines will continue to become faster and more powerful, enabling the processing of thicker materials and increasing production throughput.
Higher wattage and precision
Higher wattage choices are enabling the cutting of thicker materials at a faster rate.
Sustainability
There will be a growing emphasis on energy efficiency and reducing waste in laser cutting processes. Fiber lasers, which consume less energy than CO2 lasers, are expected to become even more popular.
Industry-Specific Applications
Laser cutting will continue to be tailored to the specific needs of different industries, including the automotive sector. This includes the development of specialized software and hardware solutions for car seat manufacturing.
Conclusion
Laser cutting technology has revolutionized car seat manufacturing, offering significant advantages in terms of precision, efficiency, design flexibility, and material versatility. Companies like Golden Laser are at the forefront of this innovation, providing advanced laser cutting solutions that empower automotive manufacturers to create high-quality, comfortable, and aesthetically pleasing car seats. As the technology continues to evolve, we can expect even greater levels of automation, speed, and sustainability, further shaping the future of automotive interiors. The integration of laser cutting into car seat production represents a significant step forward, ultimately benefiting both manufacturers and consumers.